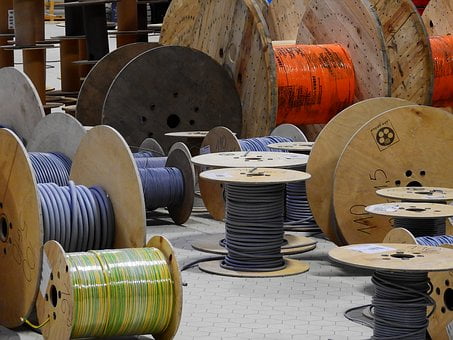
Crosslinking is a process by which polymer chains are linked together to increase their melting points. A three-dimensional polymer network is created where the molecules have been joined together will make a new nonmeltable polymer system. Now, the polymer chains lose some of their ability to move as individual chains. The result is no melting. These wires can withstand upto 110 deg to 250 deg which will not lead to melting. Some of the procedures to make wires crosslinked are continuous vulcanization, E-beam and silane linking.
Continuous Vulcanization is also called chemical crosslinking. It is usually done by passing the wire through a long pressurized tube, heated by steam – by a process continuous vulcanizing. Other methods of crosslinking include salt cure and hot air vulcanization.
Silane Linking also known as moisture linking, where polyethylene is first grafted with a mixture of vinylsilane and peroxide with the purpose of obtaining a crosslinkable polyethylene. The material can be either processed directly or stored in dry conditions for up to several months
E-beam uses ionizing energy, by an accelerated electron beam (EB). It is efficient means of crosslinking polymers which is used for wire and cable insulation and jacketing. This can also be done without heat. E-beam processing is fast, good, controllable and in a lot of cases more economical than thermal and/or chemical crosslinking
Leave a Reply